Craftsmanship inherited in the 15s
Our pottery, Kyogetsu Pottery, dedicated his time to ceramics as one of Toko nananinshu (7 professional potters) about 300 years ago (Genroku period) and built a brand, called Ōbori Sōma ware later.
Then, it has been passed down to the date and now Kondo Kyoko has succeeded to the pottery as the first female potter of the pottery in its history.
What I always care about our products as a concept is to make them closely related to the user's daily life.
Thus, I would like our receptacles to take roots in their daily life.
The way how we live our life is very various nowadays and the way how you use our products can be the same.
In other words, how about introducing a playful mind specific to the woman to your life??
Kyogetsu Pottery
The 15th KONTOKU Owner
Kondo Kyoko
Production flow
Forming clay
The essence of Ōbori Sōma ware is handmade by rokuro (potter's wheel) molding. There are several traditional ways to produce such as double structure, tobikanna (a technique that draws successive marks using bit), kikuoshi and kaimenmoyo.
In addition to this, we make products using Tatara boards and a technique called himodukuri, in which the product is molded out of clay strings.

Shaping a teacup
- Rolling rokuro and denting slowly.
- Extending the hollow to make the thickness even.
- Adjusting the thickness with a wooden spatula and a trowel.
- Smoothening the upper part with leather.
- Disconnecting the product with a string from the base.
Shaving and decoration
After molding from clay, shape the product by shaving its surface after air-drying. Then, decorate it by processing holes called hananuki and adding extra clay.
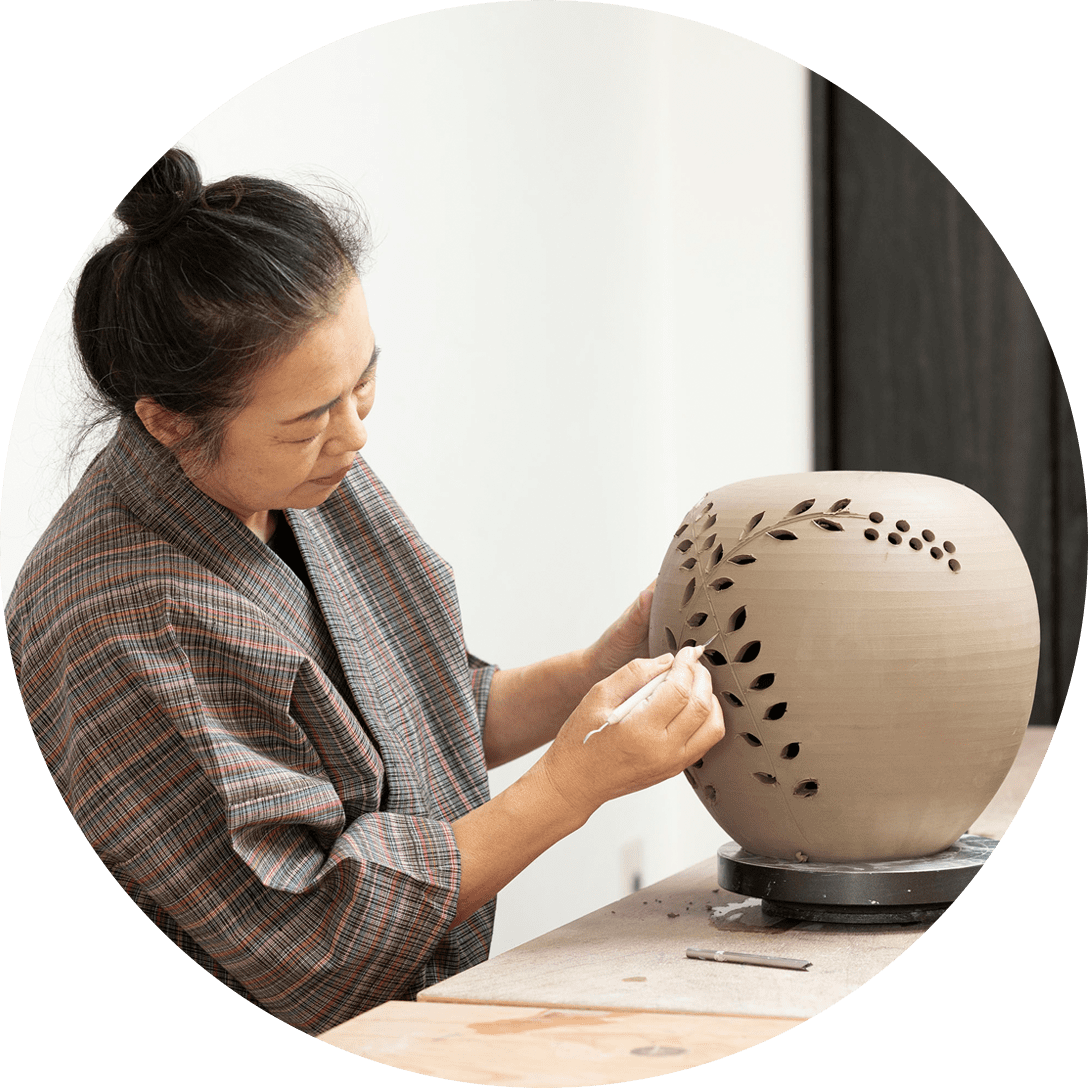
Drying
The product is dried naturally for about a month set out on a shelf after this process. The product is shrinking by one size during this process.
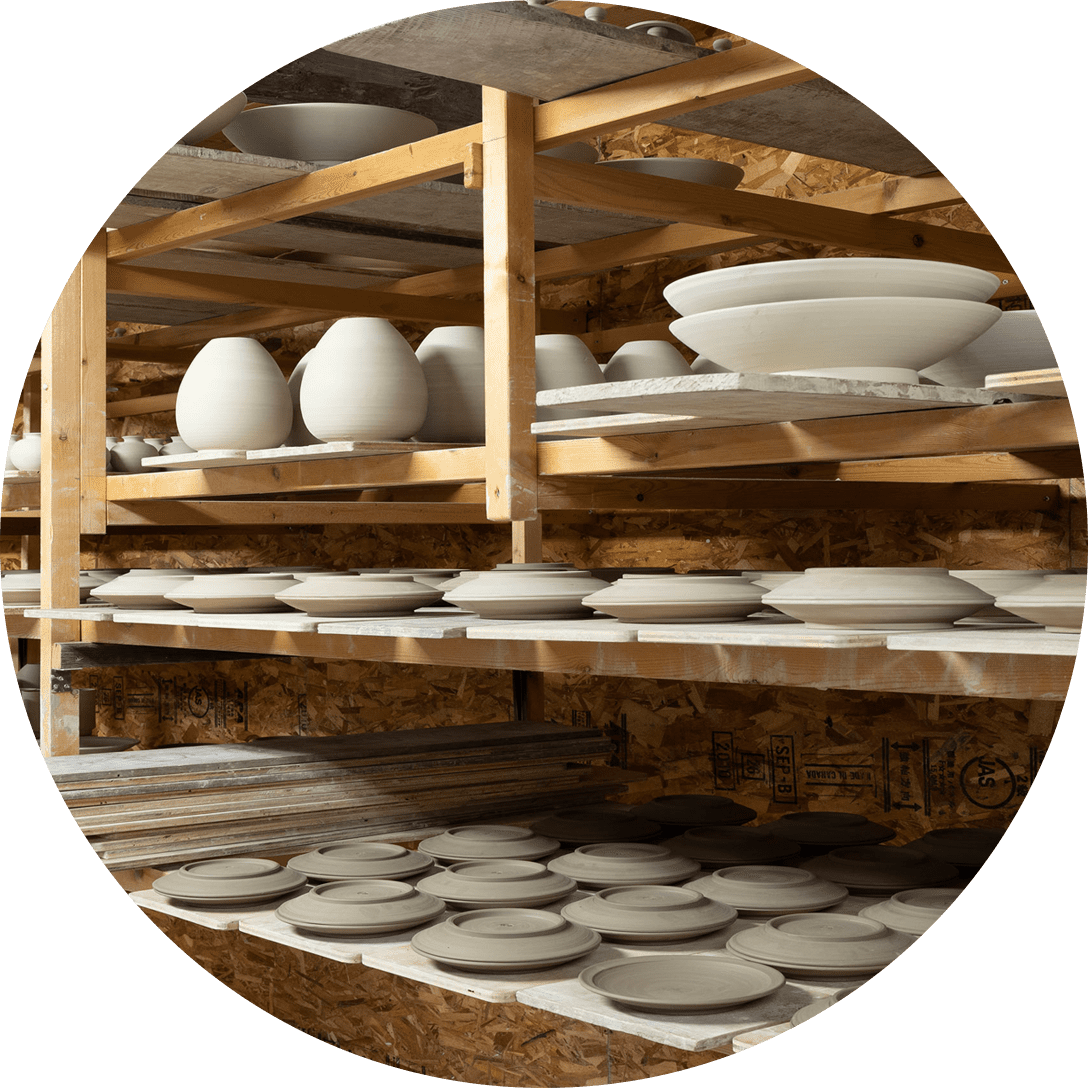
First baking(setting in a kiln)
Ōbori Sōma ware has a process that the completely dried product is once baked around 850℃ and make it unglazed pottery (this step is called suyaki) so that it is easy to glaze and paint it in the next step.
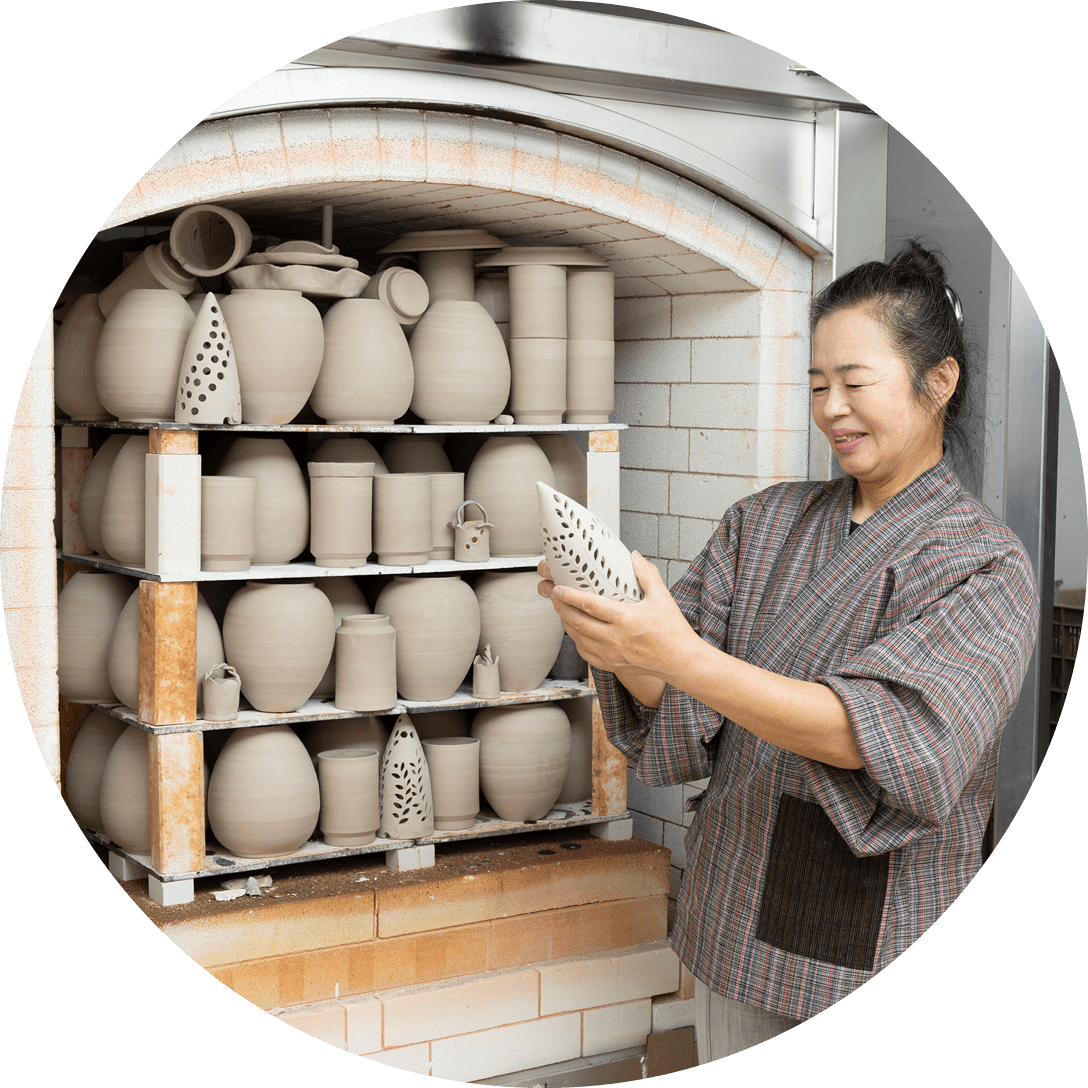
Glazing and second baking
The next step is glazing. We have traditional iron glazes and more than 10 our original uniquely blended glazes.
After glazing, the product goes to second baking.
It is baked around 1250℃ and the glaze slowly melts in a gas/electric kiln so that the chemical reaction leads to various colors and textures we pursued.

Glazing
- Glazing unglazed pottery.
- Using a special ladle to glaze neatly.
- Puting the glaze meticulously to avoid inconsistency.
- The product is still white-ish color, but it wears colors after the second baking.
From finishing to completion
Extra melted glaze is attached to the product after the second baking.
The next step is finally the finishing process. The extra glaze is carefully removed by an electric sander and sandpapers.
Also, lighting equipment such as a floor light can be equipped during this process as needed.
The process for the product is finally completed after a lot of manufacturing processes.
